Radar Level Sensor
WXR808
Features
- Can be used in stirring, steam, dust, crystallization occasions
- Fieldbus Foundation, ProfibusPA, NB-IoT, etc.
- Support Bluetooth debugging function
- Support low dielectric constant (less than 1.5) medium TBF tank bottom reflection measurement
- Support backlight display
The radar level meter may be fitted in a variety of metal and non-metal containers and pipes due to its large detection range and low beam energy. It works well in situations where there is steam, inert gas, dust, and water mist. The radar level meter is safe for both the environment and humans to use. Its benefits include not requiring on-site calibration, being unaffected by changes in the dielectric constant, and not being impacted by the specific gravity of the medium.
01
Introduction to Radar Level Sensor
In industrial manufacturing processes, radar level transmitters can detect the height of liquids in closed or open containers continuously and non-contact. The radar level transmitter may be deployed in a variety of metal and non-metal containers and pipes due to its extensive detection range and low beam energy. It works well in situations where there is steam, inert gas, dust, and water mist. The radar level transmitter is safe for both the environment and humans to use. Its benefits include not requiring on-site calibration, being unaffected by changes in the dielectric constant, and not being impacted by the specific gravity of the medium. In many industrial applications, radar level measurement is a very precise and dependable way to determine the level of liquids or solids. This method measures the distance between the surface of the substance being measured and the radar sensor using electromagnetic waves. The ability of radar level measuring to produce accurate readings even in challenging circumstances when other techniques might not work is one of its main benefits. Applications with high pressures, temperatures, or vapor or dust concentrations fall under this category.

02
Uses of Radar Level
Sensors
Industrial Process Control: Measure levels of liquids, solids, and slurries in industries like chemicals, oil & gas, and food & beverage. Water and Wastewater Management: Monitor levels in water treatment plants, reservoirs, and sewage systems. Storage Tanks: Ensure accurate level measurement in large storage tanks, including hazardous materials. Marine and Offshore: Monitor levels in ballast tanks, fuel tanks, and cargo holds on ships.
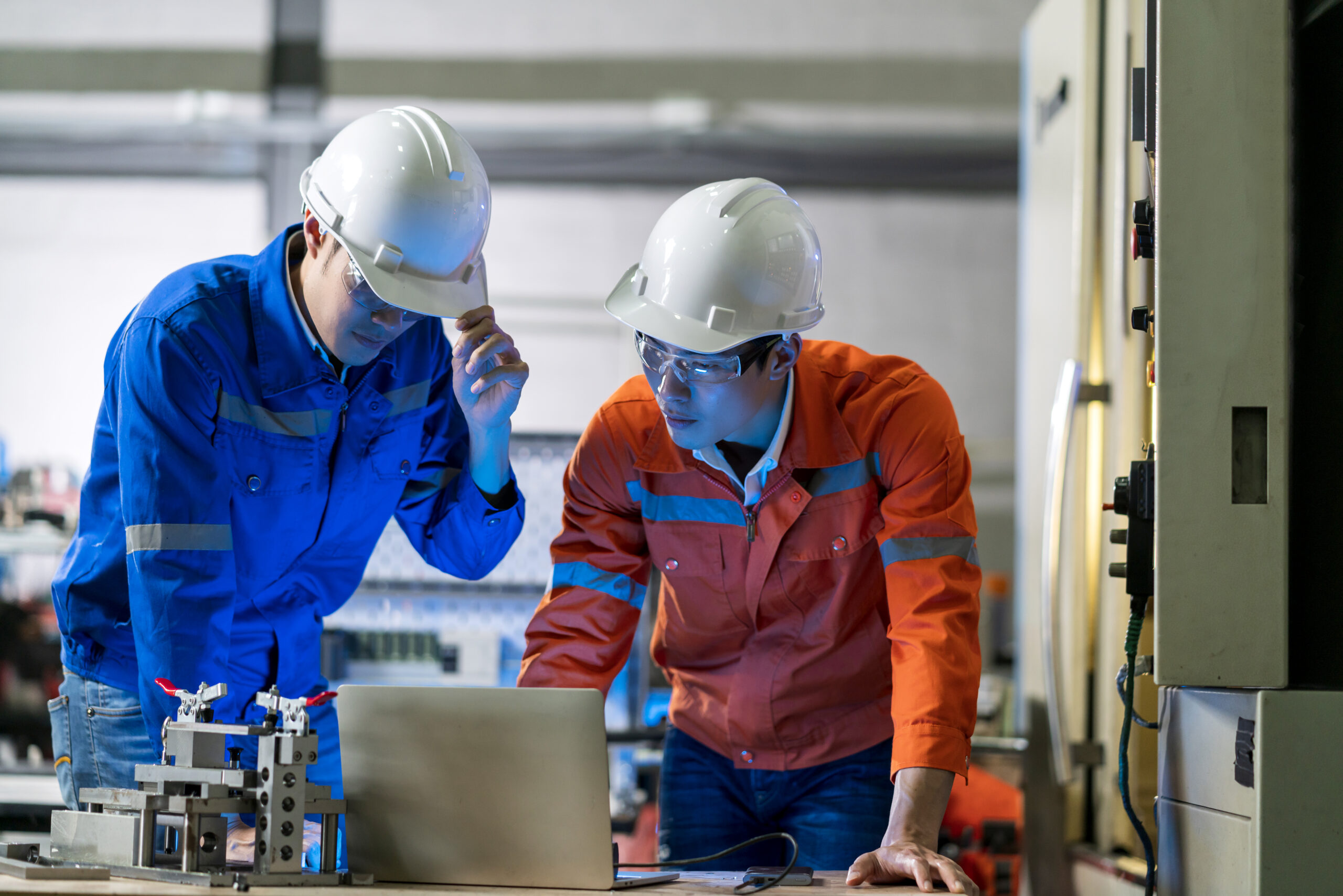
03
Application of Radar Level Sensors
Chemical Plants: For measuring levels of corrosive and hazardous liquids. Oil & Gas: Monitoring tank levels and ensuring safety in refineries. Water Treatment: Managing water levels in treatment plants and reservoirs. Food & Beverage: Ensuring consistent levels in production tanks and mixers. Mining: Measuring bulk material levels in silos and hoppers. Marine: Monitoring ballast and fuel tank levels on ships.
Principle of Radar Level Sensor
The guided wave radar emits high-frequency microwave pulses that travel along steel rods or cables for detection. These pulses come into contact with the media to be measured, and because the mutation’s dielectric constant causes reflections, some of the pulse energy is reflected back. The relationship between the transmitted pulse and the reflected pulse depends on the measured media’s distance and time interval.
Technical Specification
Product
Radar level Sensor
Model
WXR808
Measure range
0.08~30m,0.3~60m, others
Beam angle
3°/8°
Installation
Thread, Flange
Process temperature
(-40~85)℃
Process Pressure
(-0.1~0.3) MPa
Accuracy
±5mm
Ingress protection
IP67
Frequency Range
76GHz~81GHz,5GHz FMCW bandwidth
Power supply
(9~36)VDC
Communication
Modbus/HART
Humidity
≤95%RH
Enclosure
Aluminum alloy, stainless steel
Fault output
3.8mA, 4mA, 20mA, 21mA, hold
Size
Ø100*270mm
Weight
2.480Kg/2.995Kg
Cable entry
M20*1.5
Antenna type
Lens antenna/anti-corrosive antenna / flange isolated by quartz
Recommended cables
AWG18 or 0.75mm²
Minimum measured dielectric constant
≥2
Signal Output
4-20mA
RS485
Range
0-8m
Sensor
polycarbonate
Medium
Liquid
Process Connection
G1 1/2
Applications
Heating and Cooling Reactors
Disinfecting and
Sterilizing
Waste Heat Recovery Boilers
Dyeing WasteWater
Exhaust Gas Treatment
content.
Fertigation System
Accessories
Documents
User Manual_Radar level Sensor_WXR808_En_V6_2023

Wellkonix global commitment to the Chemical Industry
Wellkonix is the world leader in automation solutions to the chemical industry. As a global player, we have strong local support in any region that you run your business
Solutions
automation
Project execution
Providing solutions of every kind, at all times in chemical industries
Wellkonix engineers were all very affected person and cooperative during the early engineering and start-up phases. We labored as one team thru to the completion of this plant project