Process Controller
WC1100
Features
- Double four-digit LED display
- 7 types of dimensions available
- Standard snap-in installation
- Double four-digit LED display
- Supporting 2-way alarm
- Standard MODBUS protocol
The 1100 is an easy-to-use, single-circuit digital panel meter with a double, four-digit LED display. It can measure a variety of industrial process quantifiers, such as temperature, pressure, flow, liquid level, and humidity. It also supports input signals from transducers, thermocouples, thermal resistance, voltage, and current.
01
Introduction of Process Controller
A Process Controller is a critical component in industrial automation and control systems, designed to regulate and manage various processes to ensure they operate efficiently and within desired parameters. These devices are used across a wide range of industries, including manufacturing, chemical processing, food and beverage production, and more..An LED Display Multi-Panel Meter is a versatile and compact instrument used to measure, monitor, and display multiple electrical parameters in real-time. These meters are commonly utilized in industrial, commercial, and even residential settings where accurate monitoring of electrical systems is essential for efficiency, safety, and cost management.The meter is equipped with several LED displays, each dedicated to showing different electrical parameters simultaneously. This multi-display capability allows users to monitor various metrics at a glance without the need for multiple devices.The primary function of a process controller is to continuously monitor process variables such as temperature, pressure, flow rate, level, and other critical parameters. It compares the actual values of these variables with the desired setpoints.
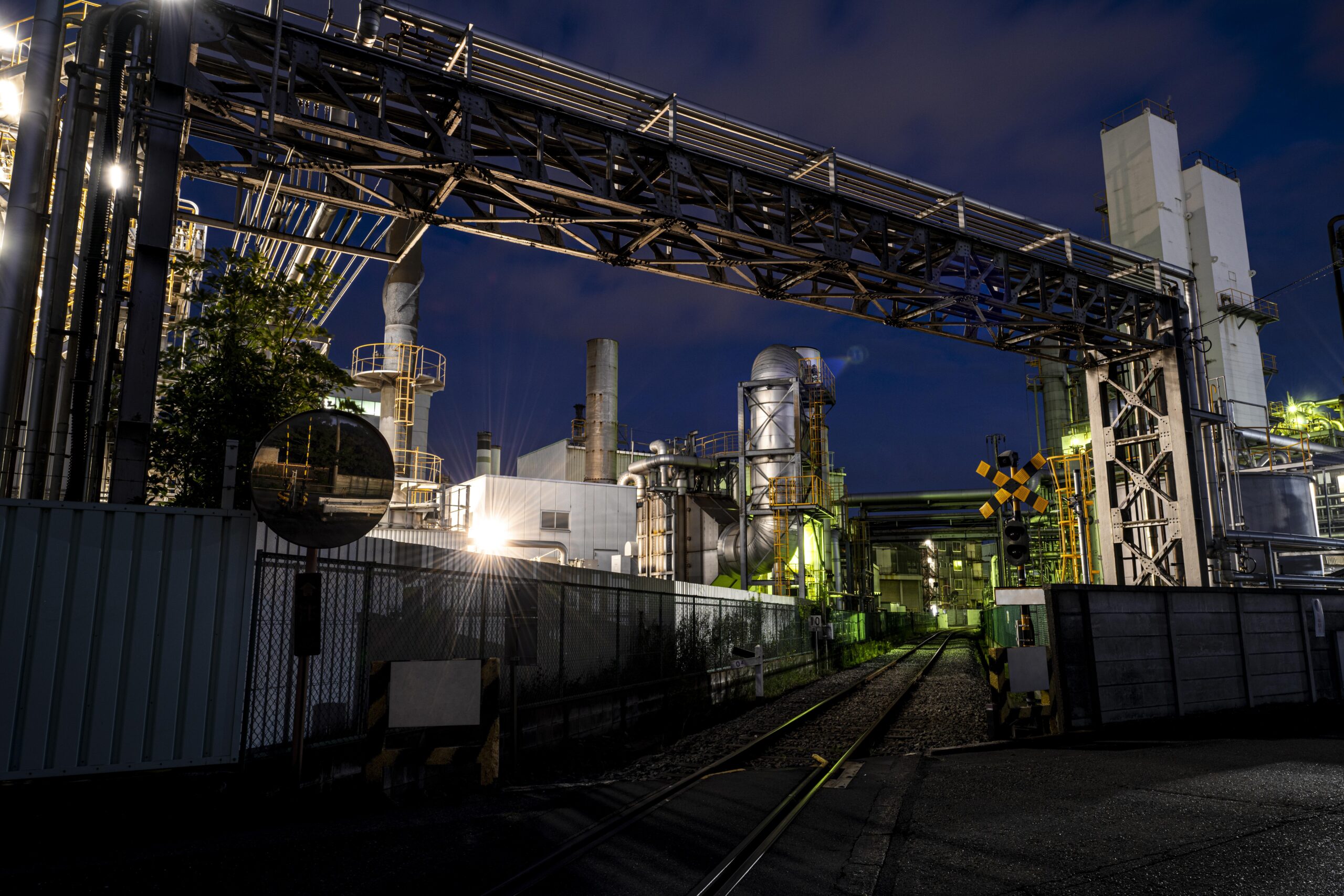
02
Application of Process Controller
Manufacturing: Controlling processes such as heating, cooling, mixing, or assembly in various manufacturing industries. Chemical Processing: Regulating the precise conditions needed for chemical reactions, such as temperature, pressure, and flow rates. Food and Beverage: Ensuring the consistent production of food products by controlling temperature, flow, and other critical parameters.

03
Uses of Process Controller
Process controllers regulate the heating and cooling elements to ensure that the temperature remains within the desired range, which is critical in processes like baking, chemical reactions, and material treatments.They adjust valves, pumps, or other pressure-regulating devices to maintain the desired pressure, preventing equipment damage and ensuring safe operation in industries like oil and gas.
Process Controller Calibration
Process controller calibration is the procedure of adjusting and fine-tuning a process controller to ensure it accurately measures and controls the process variables, such as temperature, pressure, flow, and level, according to the desired specifications. Calibration is essential for maintaining the reliability, accuracy, and consistency of the process control system.
Technical Specification
Product
Process Controller
Model
WC1100
Power Supply
220-230V AC
Relay output
2
Re-transmission signals
RS485,MODBUS-RTU
Display Size
2.8 inch
Applications
Heating and Cooling Reactors
Disinfecting and
Sterilizing
Waste Heat Recovery Boilers
Dyeing WasteWater
Exhaust Gas Treatment
content.
Fertigation System
Accessories
Documents

Wellkonix global commitment to the Chemical Industry
Wellkonix is the world leader in automation solutions to the chemical industry. As a global player, we have strong local support in any region that you run your business
Solutions
automation
Project execution
Providing solutions of every kind, at all times in chemical industries
WellKonix engineers were all very affected person and cooperative during the early engineering and start-up phases. We labored as one team thru to the completion of this plant project