
PH sensor
WPH1007
Features
- Industrial wastewater engineering
- High accuracy, fast response, good repeat-ability.
- Suspensions, varnishes, media containing solid particles
- Two-chamber system for when electrode poisons are present
- Process measurements, electroplating plants, paper industry, drinks industry
Flue gas desulfurization (FGD) and other severe environments like whitewash, seriflux, etc. can be measured for pH using the WPH1007 Flat pH electrode. An excellent sensor for measuring and analyzing liquid components during industrial automation is the pH electrode. These electrodes are renowned for using premium components and materials. The measuring electrode and the reference electrode are integrated into a single shaft in their design as combined electrodes.As an alternative, the temperature probe can also be included.
01
Industrial pH Monitoring: pH and pH Sensor Basics
1007 industrial planar PHsensor is made of ring-type polytetrafluoro-reference liquid interface, solid electrolyte and special glass sensitive film, so that the reaction speed and anti-pollution ability of the sensor are enhanced and its performance reaches the level of similar sensors in the world. The principle of pH/ORP sensor measurement is electrochemical method and galvanic battery principle. The primary battery is a system whose function is to turn chemical energy into electrical energy. The voltage of this battery is called electromotive force (EMF) which is made up of 2half-cells, of which one is called a measuring cell whose potential is related to specific ionic activity; the other is a reference half-cell, commonly known as a reference sensor, which is generally interlinked with the measuring solution and is connected to the measuring instrument. The potential difference produced by the galvanic interaction inside the sensor is transmitted to the pH controller, and the corresponding algorithm is transmitted to display the pH value.

02
Application of pH Sensor
Industrial wastewater engineering. Process measurements, electroplating plants, paper industry, drinks industry. Wastewater containing oil. Suspensions, varnishes, media containing solid particles. Two-chamber system for when electrode poisons are present. Media containing fluorides (hydrofluoric acid) up to 1000 mg/l HF. Isolated power supply design, data stability, strong anti-interference ability

03
Uses of pH Sensor
Adopt a big area PTFE liquid junction with easy maintenance and an advanced solid dielectric from across the world. Long-range reference diffusion route significantly increases electrode life in challenging conditions. Because the electrode is constructed from high-quality low-noise wire, the signal output may be produced for up to 40 meters without interference. It also has excellent precision, quick reaction times.
pH Calibration
Enter the PH calibration screen, the first PH electrode intothe4.00PH standard solution, standing for a moment, to be stable after the show, press the ENT, then the PH electrode into the 6.86PH standard solution Set the PH electrode into the 9.18PH standard solution, put it aside for a moment, after the test is stable, press ENT, the display shows the success of the calibration, the whole process of PH calibration complete
Technical Specification
Product
Flat pH sensor
Model
WPH1007
Measurement range
2~12pH
Temperature
0~60℃
Pressure range
0.4MPa
Temperature compensation
NTC10K/PT100/PT1000
Reference structure
Teflon ring/doubleliquid junction
Thread Connection
3/4NPT
Shell material
PPS
Slope
(PTS values) ≧95% (25℃)
Resistance
≦250 mΩ
Sensors
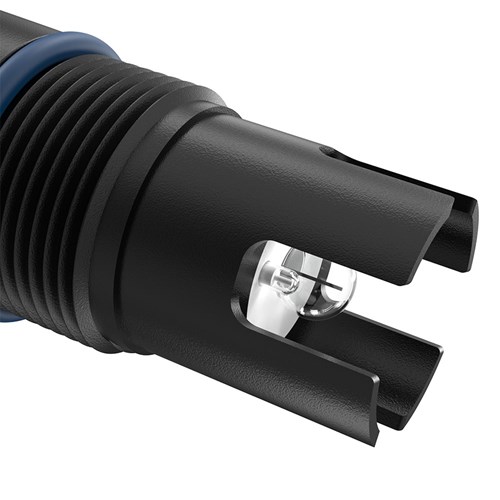
Features
Compact structure and easy installation
Isolated power supply design, data
stability, strong anti-interference ability
automatic/manual temperature
compensation
Automatically detect whether the
temperature probe is disconnected or
faulty, then switch to manual
temperature compensation
Support USA/NIST/custom pH calibration
solution, and user-defined ORP standard
solution
Communication: RS485 interface*1
(Modbus RTU protocol)
The principleof pH/ORPsensor measurement is electrochemical method and galvanic battery principle. The primary battery is a system whose function is to turn chemical energy into electrical energy. The voltage of this battery is called electromotive force (EMF) which ismade up of 2half-cells, of which one is called ameasuring cell whose potential is related to specific ionic activity; the other is a reference half-cell, commonly known as a reference sensor, which is generally interlinked with the measuring solution and is connected to the measuring instrument.The potential difference produced by the galvanic interaction inside the sensor is transmitted to the pH controller, and the corresponding algorithm is transmitted to display the pH value. WKP100 is a digital sensor with RS485 designed by our company for the aquiculture industry, which can be used to measure the change of pH/ORP value in an aqueous solution system within the range. The sensor with a standard RS485 MODBUS-RTU protocol interface, which can be connected with the host computer conducts remote communication Each sensor is manufactured with our patented Axial Ion Path® reference technology, proprietary Low-Noise & High Temp Signal Cable along with proprietary ruggedized, high temp and coat resistant glass formulations.
Applications
Heating and Cooling Reactors
Disinfecting and
Sterilizing
Waste Heat Recovery Boilers
Dyeing WasteWater
Exhaust Gas Treatment
content.
Fertigation System
Accessories
Documents

Wellkonix global commitment to the Chemical Industry
Wellkonix is the world leader in automation solutions to the chemical industry. As a global player, we have strong local support in any region that you run your business
Solutions
automation
Project execution
Providing solutions of every kind, at all times in chemical industries
WellKonix engineers were all very affected person and cooperative during the early engineering and start-up phases. We labored as one team thru to the completion of this plant project